Qu’est-ce que l’industrie 4.0 ?
Industrie 4.0 ou l’usine du futur correspond à l’évolution la plus récente des techniques de fabrication. L’usine 4.0 est portée par l’introduction des méthodes de fabrication qui exploitent la réalité augmentée, les objets connectés, l’impression 3D, les robots… Les notions de cloud et de big data prennent tout leur sens dans l’usine du futur qui attribue une place prépondérante à l’intelligence artificielle. C’est une usine qui fonctionne en connectant des objets réels au numérique et à l’Homme. Elle a pour vocation de permettre la personnalisation des produits. En effet, les nouvelles technologies fournissent les outils permettant de satisfaire les attentes des consommateurs qui sont à la recherche de produits uniques mais qui restent abordables.
La quatrième révolution industrielle permet d’optimiser la flexibilité des processus et d’augmenter leur fiabilité tout en maintenant une capacité de production élevée. Les avancées digitales offrent également la possibilité de conserver des coûts de production maîtrisés malgré la faible quantité d’exemplaires usinés et commercialisés en réponse aux besoins de personnalisation.
L’Industrie 4.0 se définit donc comme un vecteur de réduction des consommations énergétiques et des dépenses liées à la main d’œuvre pour donner naissance à des produits qualitatifs, uniques et moins onéreux.
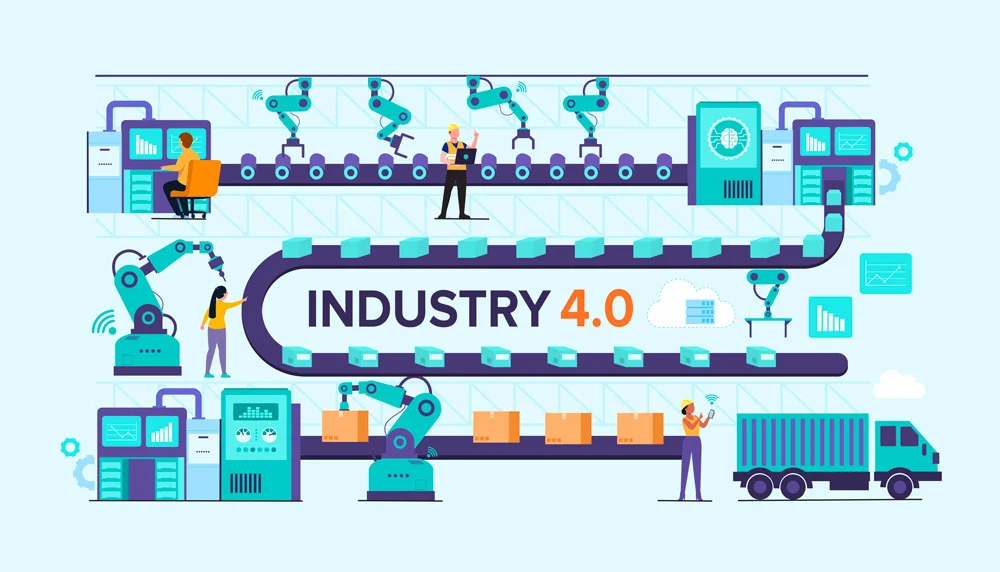
D’où vient le nom «industrie 4.0»?
Sous l’impulsion des progrès technologiques, une nouvelle révolution industrielle est en train de s’opérer. On parle de l’Industrie 4.0 qui est incontestablement orientée vers le futur. Mais de quoi s’agit-il au juste ? Voici les éléments essentiels concernant cette industrie nouvelle.
Retour sur la naissance de l’industrie du futur
1ère révolution industrielle
L’industrie 1.0 est née en 1765, portée par l’essor de la production mécanique. C’est la première révolution industrielle. Lorsque James Watt met la première machine à vapeur au point en 1769, il devient plus facile d’exploiter le charbon pour faire tourner les usines. Les machines se substituent progressivement à l’artisanat, ce qui permet d’augmenter la vitesse de production. A partir de là, les objets commencent à être fabriqués en petites séries.
2nd révolution industrielle
La seconde révolution industrielle qui correspond à la naissance de l’industrie 2.0 date de 1870. En effet, les énergies pétrolières et électriques sont davantage exploitées vers la fin du XIXe siècle. Les processus de fabrication gagnent automatiquement en modernité, ce qui permet de booster les cadences de conception. Les industries chimiques et automobiles remplacent les machines à vapeur par des appareils électriques. Le taylorisme commence à être appliqué, ce qui permet de rentabiliser le recrutement d’ouvriers non qualifiés. Les nouvelles énergies exploitées par l’industrie 2.0 permettent de lancer la production de masse, c’est-à-dire la fabrication en série de plusieurs produits identiques.
3ème révolution industrielle
Le milieu du XXe siècle est marqué par la troisième révolution industrielle, propulsée par l’automatisation et la mondialisation. C’est plus précisément à partir de 1969 que les changements majeurs s’opèrent. L’avènement de l’informatique, le développement de l’électronique, sans négliger la réduction des coûts des télécommunications permettent en effet de modifier le mode de fonctionnement au sein des usines. Plus concrètement, les ouvriers sont délestés des tâches ardues et répétitives grâce à l’adoption du système d’automatisation. La robotique naît parallèlement à l’industrie 3.0 qui favorise les productions en grandes séries.
Certains observateurs situent l’apparition de l’industrie 3.0 au début du XXIe siècle. Selon leurs analyses, c’est la transition écologique qui serait à l’origine des changements. L’exploitation des énergies renouvelables et le développement de la technologie numérique sous des formes résolument innovantes seraient alors les éléments marquants de cette troisième révolution portée par l’exploitation des énergies propres.
4ème révolution industrielle :
L’Industrie 4.0 se développe depuis 2011 grâce à la numérisation. Le terme est apparu en Allemagne, lors de la Foire de Hanovre. La nouvelle révolution implique l’exploitation des technologies numériques pour offrir des produits/services personnalisés aux consommateurs, sans forcément engager des investissements conséquents. L’industrie ou usine 4.0 se situe à la croisée des objets réels et digitaux. Il s’agit d’une industrie connectée qui exploite les différents aspects de l’intelligence artificielle, à la réalité virtuelle et tout ce que la technologie numérique met à la disposition des entreprises souhaitant gagner en performance. Plusieurs systèmes numériques fonctionnent en interconnexion afin de faire progresser la vitesse de production, la fiabilité des processus et la sécurité des équipes. Les stratégies adoptées permettent automatiquement aux industries de participer à la transition écologique tout en plaçant les consommateurs au centre de leurs préoccupations.
L’industrie 4.0 est donc celle qui balaie progressivement les frontières entre le physique et le digital dans l’optique de faire évoluer le système manufacturier.
Les composants de l’industrie 4.0
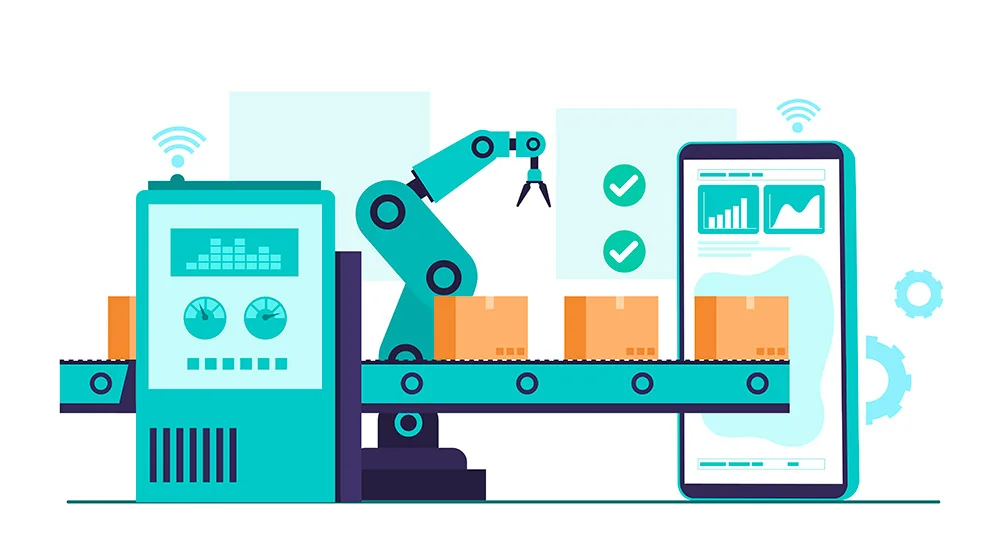
Popularisée par les médias, l’appellation industrie 4.0 est un concept qui a pour ambition d’augmenter la productivité des entreprises qui l’intègrent dans leur fonctionnement. Cette industrie du futur se place au cœur de la production et permet d’y apporter des améliorations significatives.
La numérisation
L’industrie 4.0 incorpore l’utilisation de plusieurs technologies telles que l’Internet des objets (IoT), l’impression 3D, la réalité augmentée, le cloud computing, l’analytique big data et l’intelligence artificielle. Les usines 4.0 sont dotées de capteurs à la pointe, de logiciels et de robotique. Ces éléments ont pour fonction de recueillir et d’analyser les données, en vue d’amener à prendre les décisions les plus pertinentes du point de vue logistique. Par ailleurs, il est possible d’associer les données de production à celles des stocks, des systèmes de planification des moyens de l’entreprise (ERP) et des centres de support entre elles. On peut ainsi rendre visibles de précieuses informations qui, dans les systèmes précédents, restaient compartimentés.
L’automatisation
Avec la numérisation des entreprises, on observe le développement de l’automatisation, de la maintenance prédictive et l’amélioration des procédés opérationnels. Les performances et l’expérience client atteignent en outre des degrés qu’on ne pouvait imaginer jusqu’à présent.
Dans l’usine intelligente, les capteurs intégrés jouent un rôle prépondérant, dans la mesure où ils procurent une transparence étendue des actifs de production. Leur efficacité pour anticiper les pannes des machines permet d’assurer la continuité au niveau de la production.
L’usine intelligente
L’IoT, les systèmes cyber-physiques, le cloud computing et l’analytique big data sont les principales technologies sur lesquelles se base l’industrie 4.0. En combinant ces technologies, on obtient l’usine connectée dont l’objectif est de permettre aux objets de communiquer entre eux et de bénéficier d’une certaine autonomie. Le contrôle dans la fabrication s’effectue par le biais d’informations visuelles fondées sur l’IA et non plus manuellement. On parle alors de réalité augmentée.
L’impression 3D sert à la fabrication de produits sur mesure à partir des instructions données par le client. Il en résulte une amélioration au niveau des étapes de production et de la qualité. Le risque d’erreur, quant à lui, devient moindre. Qui plus est, la génération des déchets s’en trouve également diminuée.
Client connecté
Le fabricant peut prévoir de munir les produits qu’il vend à ses clients de capteurs intelligents. Il est ainsi possible d’en faire le suivi, notamment pour ce qui concerne la maintenance ou encore les défaillances. Le client est alors averti immédiatement et est en mesure de pallier les problèmes.
En outre, pour garder le contact avec les clients ou les fournisseurs, il peut être envisagé la mise en place d’un extranet ou d’un système EDI (Échange de données informatisées).
Les applications pour l’industrie 4.0
En tant que professionnel de l’industrie ou confronté à des problématiques industrielles, vous songez certainement à numériser certaines pratiques, ou à faire évoluer votre activité vers le monde du digital.
Cette nouvelle approche met à la disposition des entreprises de nombreux outils permettant notamment d’optimiser la ligne de production. Pour mieux comprendre les avantages procurés par le passage à l’industrie 4.0, notamment en termes de coût et de complexité, voici quelques exemples récurrents d’applications.
Des économies de papier et de consommables
La numérisation des contenus permet aux entreprises d’optimiser durablement la gestion des documents : en passant du format analogique au format numérique, chaque collaborateur contribue à réduire le temps passé sur des tâches redondantes. Les erreurs, souvent causées par des données périmées, sont considérablement réduites. Numériser l’activité devient dès lors une question de survie pour les structures désireuses de rester compétitives.
Optimisation des procédés, IoT et contrôle en temps réel
La digitalisation s’accompagne très souvent de la mise en place de logiciels de contrôle ou d’analyse avancée, permettant d’améliorer la production. Dans le même temps, les machines et équipements peuvent être équipés de capteurs sans fil, de manière à obtenir un suivi précis de la production et recueillir des données en temps réels. C’est le principe-mêle de l’IoT (ou Internet des objets) permettant une haute connectivité.
L’expérimentation de l’impression 3D
La digitalisation permet d’introduire dans les process de nouvelles machines et donc, de nouvelles méthodes pour concevoir des produits toujours plus spécifiques et hautement personnalisés. C’est le cas par exemple des imprimantes 3D, permettant de produire très rapidement des prototypes et de fabriquer des formes complexes en tenant compte des spécifications du client à chaque instant.
Une connectivité étendue des produits à Internet
Grâce à la digitalisation, chaque produit conçu en usine peut être équipé de capteurs, afin d’en surveiller l’utilisation, effectuer l’entretien et signaler des problèmes éventuels. Les clients sont donc avertis en temps réel en cas de défaillance. Selon l’usage, les produits « intelligents » peuvent également embarquer des services afin de faire évoluer le modèle d’origine.
L’intégration de réseaux informatiques
Les nouvelles technologies de numérisation permettent le recours au commerce interentreprise. L’emploi d’un extranet ou d’un système d’échange de données informatisé (EDI) permet aux entreprises de demeurer en contact avec leurs clients, fournisseurs et partenaires. Pour tout ce qui touche au commerce grand public, on pourra également avoir déployer un site Web transactionnel.
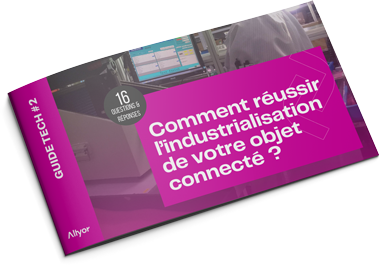
Comment réussir l’industrialisation de votre objet connecté ?
L’industrialisation est une étape centrale pour le développement et la mise en production d’un produit électronique. Dans ce guide, nos experts ont rassemblé 16 points clés pour vous faire comprendre les enjeux de cette phase.
Conception, industrialisation, production, remanufacture, nous proposons un accompagnement global continu et sur mesure pour une maîtrise et une réussite de votre projet.
01
Accompagnement à l’innovation
_Nous bâtissons des bases solides pour votre projet industriel
02
Conception mécanique & électronique
_Nous donnons vie durablement
à votre produit
03
Industrialisation
_Nous industrialisons votre produit pour fiabiliser votre production
04
Production
_Nous mettons en œuvre votre ligne de production robuste
05
Remanufacture
_Nous accompagnons les différentes vies de votre produit