Fabrication pièce en série : pourquoi choisir l’injection plastique ?
L’injection plastique, également appelée moulage par injection, est un procédé de transformation des matières thermoplastiques.
Fabrication pièce en série : le concept de l’injection plastique
Ce process est particulièrement adapté à la production en série, et est utilisable pour tout type de séries à partir de quelques centaines de pièces.
Le dimensionnement du moule se fera en fonction de la quantité annuelle à produire :
- Nombre d’empreintes (=nombre de pièces produites à chaque moulée)
- Qualité, dureté de l’acier utilisé
La transformation repose sur le principe de plastification de la matière, introduite en granulés, cette matière rendue visqueuse étant injectée sous haute pression dans le moule.
Les intérêts économiques et techniques
L’injection plastique présente un double intérêt économique et technique. La matière est relativement peu coûteuse, les temps de fabrication sont réduits et le résultat est qualitatif. Une pièce plastique réalisée avec ce procédé bénéficiera d’un état de surface adapté (surfaces poli-mirroirs ou grainées), sans retouches nécessaires, et avec un bon ratio poids / propriétés mécaniques.
L’injection plastique permet une grande variété de formes. La variété des matières permet par ailleurs d’envisager la production de pièces d’aspects et de pièces techniques.
Comment fonctionne l’injection plastique ?
La transformation de pièces en séries par injection plastique se fait grâce à une presse à injecter, qui permet la fabrication d’objets finis.
2 parties principales constituent une presse à injecter :
La matière plastique, sous forme de granulés, est tout d’abord introduite dans la trémie de la presse à injecter.
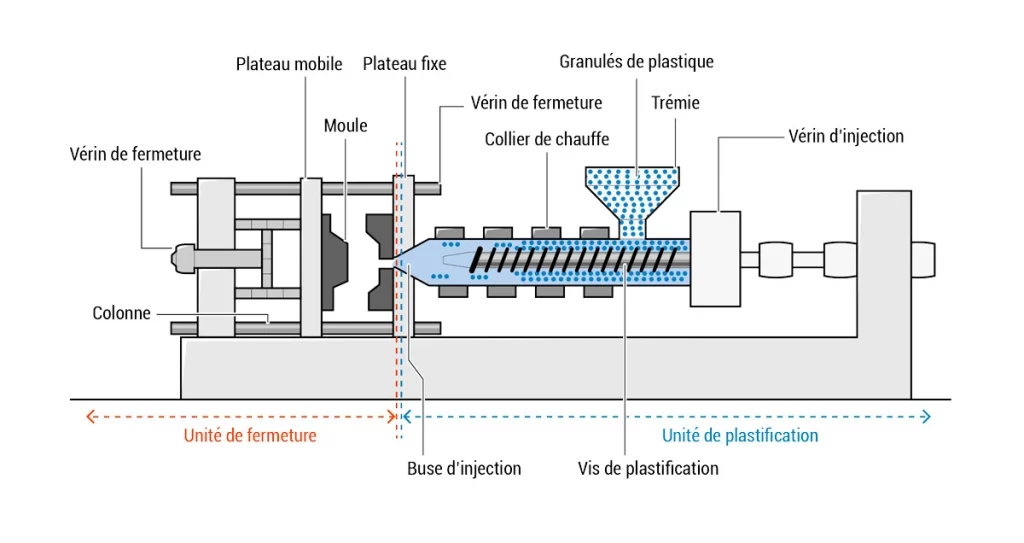
Partie droite : l’unité de plastification
Une vis sans fin, dans un fourreau chauffant, placée sous la trémie, tourne et fait ainsi avancer la matière jusqu’au bout de la vis. Les granulés sont ainsi fondus tout au long du parcours, pour avoir une matière homogène avec la bonne viscosité en bout de vis. Cette phase d’acheminement de la matière en bout de vis s’appelle le dosage.
La température du fourreau dépend de la matière. De 180 degrés à + de 300 degrés pour certaines matières.
Le piston permet de transférer la matière du bout de la vis à l’intérieur du moule.
La matière passe alors au travers d’une buse d’injection, élément mécanique faisant le lien entre la vis d’injection et le moule.
La pression d’injection , en bout de vis, peut aller de 800 à + de 3000 bars.
Une fois la matière injectée dans le moule, celle-ci va se refroidir , en se rétractant autour de l’empreinte noyau. Une fois la pièce à température suffisamment basse, un jeu d’éjecteurs (sortes de cylindres métalliques fins translatant indépendamment des empreintes et générant les petits cercles que l’on voit souvent sur les pièces plastiques !) va être actionné et permettre d’éjecter la pièce hors du moule . La pièce peut être reprise par un opérateur, un robot ou tomber en vrac dans une unité de conditionnement.
Le moule peut alors se refermer et le cycle suivant démarre. (le dosage se fait en partie en temps masqué pendant le refroidissement / l’ouverture et l’éjection des pièces)
Partie gauche : l’unité de fermeture
La pression d’injection génère un effort tendant à ouvrir le moule en son plan de joint.
Pour contrer cet effort, l’unité de fermeture, via un système de vérins hydrauliques et de genouillères, assure le maintien fermé du moule. On parle de tonnage de presse (80 tonnes , 150 tonnes, 500 tonnes par exemple), c’est un abus de langage donnant la force maximale de verrouillage de la presse. (Exemple : 150 tonnes de fermeture correspondent à ~1500 N de force)
La force théorique de verrouillage nécessaire se calcule en multipliant la surface projetée des pièces injectées (par moulée) par la pression matière.
Exemple :
Une matière injectée à une pression théorique de 800 bars
Un moule 2 empreintes, dont la surface projetée par pièce est de 100cm2
La pression théorique de verrouillage est égal à : (800 x 100 x 2 (2 empreintes) )/1000 x 1,15 (facteur de sécurité) = 18
La structure d’un moule pour l’injection plastique
Le moule est un élément indispensable dans la fabrication d’objets finis par injection plastique. Également appelé outillage, c’est lui qui permet de modeler le plastique pour lui donner sa forme définitive.
Un outillage peut peser de quelques centaines de kg à plusieurs tonnes, et est constitué d’une carcasse et d’empreintes. Les empreintes sont le cœur du moule, la partie moulante du produit.
La carcasse est l’enveloppe permettant d’héberger ces empreintes et d’assurer toutes les fonctions indispensables du moule :
- Bridage sur la presse
- Canaux d’injection
- Circuits de régulation
- Plaques d’éjection etc.
L’outillage utilisé dans la fabrication d’une pièce plastique est séparé en deux parties principales. La première partie du moule est fixe, tandis que la seconde est mobile, pour permettre l’ouverture de l’outillage et l’éjection de la pièce fabriquée.
Schématiquement, cela semble donc simple ! Mais un outillage d’injection est un outil complexe pour beaucoup de raisons :
- Le dimensionnement des fonctions d’injection (dimensionnement des canaux, des points d’injection) est essentiel à la faisabilité et à la qualité de la pièce
- De la même manière, les canaux de maintien à température du moule doivent être bien positionnés et dimensionnés
La prise en compte de ces aspects rhéologie et thermodynamique est essentielle !
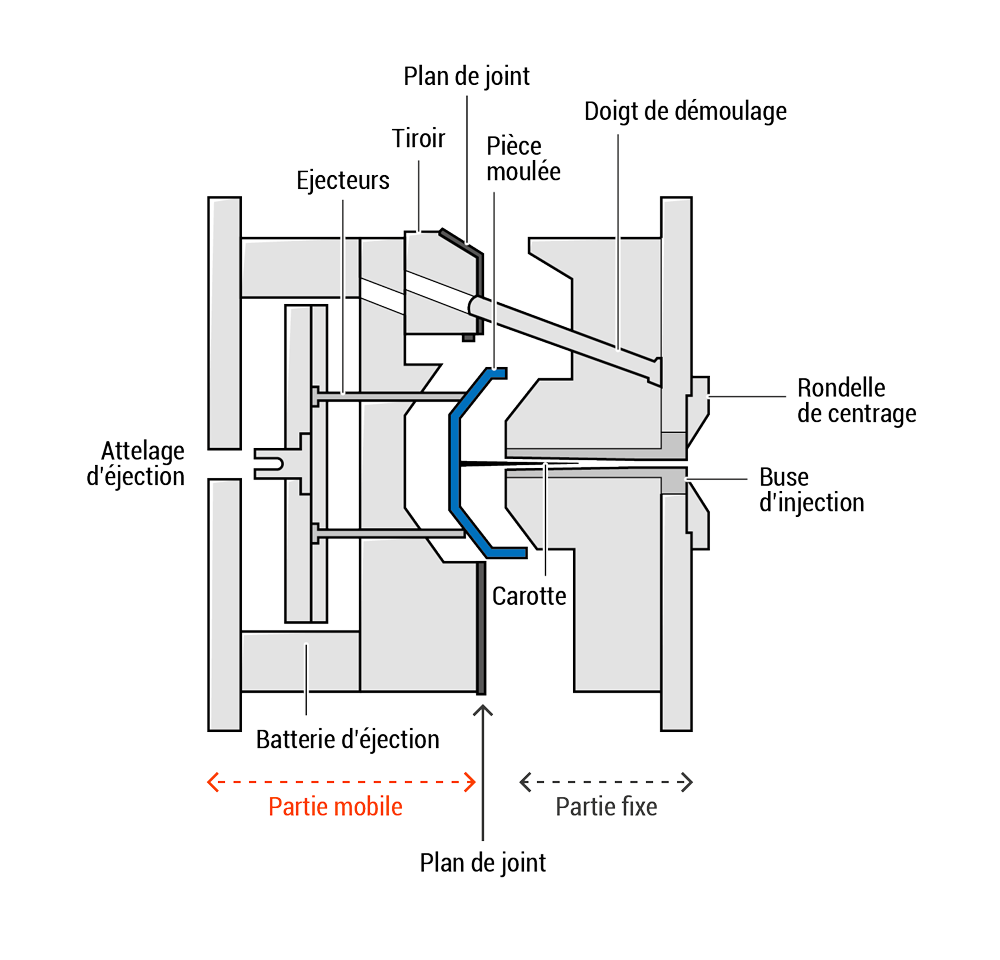
De plus, les empreintes sont un puzzle de dizaines voire centaines de pièces mécaniques, usinées avec précision. Les étapes sont nombreuses : élaboration des blocs empreintes et pavés / usinages bruts / découpe-fil / traitement thermiques / érosion etc.
Les phases d’ajustage (le montage de l’ensemble des pièce de ce puzzle de métal !) sont minutieuses et nécessitent une forte expérience du mouliste.
Les éléments mécaniques (permettant le moulage de formes en contre-dépouille), présentent une difficulté de plus, puisque ces pièces sont en mouvement et devront être parfaitement ajustées et pensées pour pouvoir assurer des mouvements répétés.
Les caractéristiques d’une pièce injectée
L’aspect des pièces obtenues en injection plastique présente quelques particularités. Une pièce injectée présente ainsi quatre caractéristiques typiques de ce processus : un point d’injection, des traces d’éjecteurs, des lignes de plan de joint (principal et secondaire) des dépouilles.
Chacune de ces caractéristiques a une raison d’être précise. Ainsi, le point d’injection marque l’entrée de la matière dans la pièce. Les traces d’éjecteurs sont dues aux éjecteurs affleurants aux empreintes. La ligne de plan de joint principal correspond à l’emplacement de la fermeture du moule (partie fixe et partie mobile). Les lignes de plan de joint secondaires sont dues aux tiroirs, cales montantes permettant la réalisation des formes en contre-dépouille. Enfin, les dépouilles aident à sortir la pièce plastique de l’outillage, sans l’abîmer.
Le point d’injection
Toute pièce injectée a forcément un point d’injection. Il marque l’endroit où la buse d’injection a introduit la matière plastique dans l’outillage. Le point d’injection a souvent la forme d’une nappe ou encore d’un petit picot. Il peut aussi bien se situer au centre de la pièce que sur un bord extérieur. La conception de l’outillage qui va être utilisé dans le processus de fabrication doit prendre en compte le point d’injection, pour décider de son aspect et de son emplacement. Cet aspect et cet emplacement ne sont pas uniquement basés sur des critères esthétiques. Du bon positionnement et dimensionnement des canaux d’injection et du point d’injection dépendra le bon remplissage du moule .
Un emplacement central du point d’injection va aider à bien équilibrer les pressions au moment de l’injection. Cette solution aide aussi à optimiser les dimensions de l’outillage. Elle présente cependant quelques inconvénients, notamment esthétiques : la carotte d’injection est alors plus difficile à couper sur les moules qui ne sont pas équipés d’une buse chaude. L’utilisation d’une buse chaude ou d’un bloc chaud règle le problème, mais cette option coûteuse n’est justifiable que pour des quantités importantes.
Lorsque le point d’injection est placé sur le bord de la pièce fabriquée, la coupe du canal d’injection se fait plus facilement, souvent de manière automatique à l’ouverture du moule (on parle de seuil d’injection en sous-marin). Ce type de point d’injection permet également de réaliser des moules multi-empreintes de façon moins onéreuse et d’avoir un point sous-marin pour un dégrappage automatique. Il présente, lui aussi, quelques points d’attention : il faut veiller au bon équilibre du moule, de telle manière que le remplissage se fasse de manière homogène.
La fin de remplissage est notamment primordiale : il faut éviter de finir de remplir des zones du moule trop tôt par rapport au reste du moule. Cela générerait alors un surcompactage de la matière dans ces zones, et des déformations, des bavures, une fragilité, etc. Tout cela se simule à l’aide de logiciels de rhéologie.
Les traces d’éjecteurs
Avec la méthode de l’injection plastique, la matière utilisée va subir de très fortes pressions au moment de l’injection dans l’outillage. Elle se retrouve compressée et se rétracte de 0,5 % à 3,0 % au moment du refroidissement, se resserrant alors sur le noyau central. Afin de démouler la pièce fabriquée, il faut la pousser hors de l’outillage grâce à des éjecteurs, commandés par la batterie d’éjection.
Des découpes dans l’empreinte permettent le passage de ces éjecteurs. Une découpe dans l’acier provoque nécessairement une trace sur la pièce plastique injectée. Ces petites traces sont souvent circulaires ou rectangulaires. Il est important de savoir où les traces d’éjecteurs vont se situer, que ce soit pour s’assurer du bon aspect de la pièce ou pour garantir ses propriétés techniques. D’autres solutions d’éjection sont possibles, notamment des plaques dévétisseuses, une éjection par air comprimé ou bien des tiroirs latéraux. Ces méthodes sont cependant plus coûteuses et sont donc à réserver pour des cas bien spécifiques.
Les lignes de plan de joint
La rencontre des différentes parties de l’outillage va venir former une ligne sur la pièce plastique. C’est ce qu’on appelle la ligne de plan de joint. Cette ligne fine et continue fait le tour de la pièce.
La conception du moule doit donc prendre la ligne de plan de joint en compte. Pour une pièce d’aspect, notamment, il faudra trouver l’endroit idéal pour qu’elle soit la moins visible . Elle peut, par exemple, être placée sur la base de la pièce si celle-ci n’est pas visible. Elle peut aussi être fondue entre deux états de surface ou être posée sur une simple boursouflure décorative. Selon la pièce voulue, décider de l’emplacement de la ligne de plan de joint sera donc plus ou moins complexe. Le mouliste devra prendre en compte l’utilisation qui sera faite de la pièce afin de faire le meilleur choix.
Les dépouilles
Les dépouilles sont des angles placés sur les faces de la pièce plastique. Elles permettent de réaliser un bon démoulage, en réduisant les frottements. La matière, en se rétractant, se retrouve soumise au noyau du moule et, en l’absence de dépouilles, la pièce sera difficile à extraire sans être déformée, cassée ou rayée.
Une dépouille forme généralement un angle compris entre 1,0° et 5,0°. Sa mesure exacte dépendra de la matière utilisée, de la texture, des dimensions de la pièce ou encore de la méthode d’éjection choisie. Les dépouilles doivent être pensées dès la conception de la pièce.
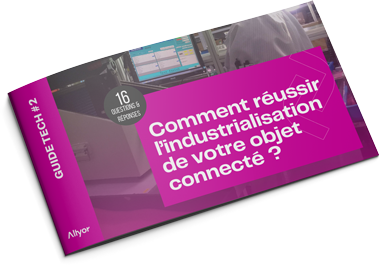
Comment réussir l’industrialisation de votre objet connecté ?
L’industrialisation est une étape centrale pour le développement et la mise en production d’un produit électronique. Dans ce guide, nos experts ont rassemblé 16 points clés pour vous faire comprendre les enjeux de cette phase.
L’injection plastique chez Altyor
Nous disposons d’un atelier hébergé dans notre usine d’Altyor Shanghai, et un réseau d’injecteurs en France et en Europe.
Notre atelier de Shanghai est capable d’injecter une grande variété de matières : ABS, PC, PP, PA, etc
tonnages de 80 à 500 t